塑膠射出成型全流程包括模具設計、材料選擇、成型工序、品質檢測及完工處理,
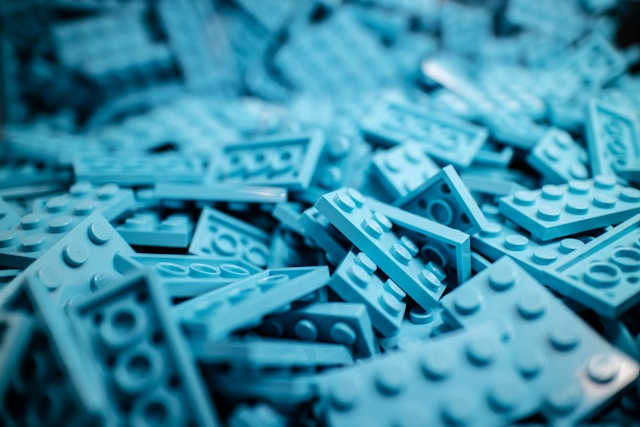
塑膠射出成型是當代工業製造中的核心技術之一,廣泛應用於電子、汽車、消費品及醫療器材等各領域。從模具設計、材料選擇、射出成型到最終產品完工,每個環節都決定著產品的品質和效能。
1. 模具開發:產品製作的基石
塑膠射出模具成型的第一步就是模具開發,這是影響產品精度、外觀及使用壽命的關鍵因素。設計師需根據產品的結構、尺寸要求及材料特性,進行精密的模具設計,透過精確的模具設計,能夠避免生產中常見的翹曲、變形等問題,提升產品成型的成功率。以下是模具設計的幾個重要環節:
‧產品分析:
了解產品的使用環境、尺寸及精度要求,確定模具結構及排氣方案。
‧模具材料選擇:
模具通常使用高硬度合金或不鏽鋼,以確保其耐用性和抗磨損能力。
‧冷卻設計:
模具內部設置冷卻水道,幫助塑膠製品在成型後快速冷卻,縮短生產周期。
‧模具結構確認:
包括選擇頂出系統、側向滑塊設計及頂針佈局等,這些設計能確保產品從模具中順利取出。
2. 材料選擇:產品特性的關鍵
在模具設計完成後,選擇適合的塑膠原材料同樣重要。不同材料具有不同的物理性質、化學耐性及加工特性,合適的材料選擇,能保證塑膠製品的使用壽命和穩定性,使其在市場上具有競爭力。選材時需考量以下因素:
‧泛用塑膠與工程塑膠:
泛用塑膠如PP、PE、PVC,價格低、應用廣泛;工程塑膠如ABS、PC、POM,強度高、耐熱性好,適合精密元件。
‧材料的流動性與耐熱性:
流動性決定了材料在模具中是否能填充到位,而耐熱性則關係到材料在不同環境下的穩定性。
‧顏色與添加劑:
根據產品用途和客戶需求,可選擇透明、抗紫外線、防火等添加劑。
3. 射出成型:塑膠製品的誕生
塑膠射出成型是將塑膠顆粒加熱至熔融狀態,然後以高壓將熔融塑膠射入塑膠模具,冷卻後形成固定形狀的製品。這一過程需經過數個步驟:
‧材料加熱:
材料在加熱筒內加熱至熔融,常見加熱溫度在200°C至300°C不等,根據材料特性調整溫度。
‧注射過程:
透過螺桿將熔融塑膠推入模具,並確保壓力足夠,讓塑膠流遍模具的每個角落。
‧冷卻固化:
塑膠模具內冷卻,使其固化並最終定型。冷卻時間與模具溫度、材料種類及產品厚度有關。
‧頂出脫模:
當冷卻完成後,透過模具內的頂針將製品取出,並確保其不損傷產品表面。
這個過程需要確保每一步都準確無誤,以避免氣泡、縮水、翹曲等品質問題。
4. 品質檢測:保證產品無瑕疵
射出成型後的產品,需經過嚴格的品質檢測,以確保每件製品符合設計和客戶的要求。檢測項目包括:
‧外觀檢查:
確認製品表面是否光滑,有無刮痕、裂痕或變形等瑕疵。
‧尺寸測量:
檢查製品尺寸是否符合設計規格,避免因縮水或偏差造成的質量問題。
‧材料特性測試:
塑膠模具根據製品用途進行耐熱性、耐化學性或抗UV測試,確保產品符合環境需求。
5. 完工處理:提升產品附加值
產品成型後,常需進行完工處理,以增加產品的美觀性和實用性。這些後加工工序不僅增加了產品的附加值,也幫助客戶提高品牌的整體形象。以下是幾種常見的後加工方式:
‧模內貼標加工(IML):
在射出成型時將標籤融入產品表面,提升產品的外觀和標識度,且不易脫落。
‧燙金印刷加工:
在產品表面進行燙金處理,適合需要高端質感的產品,增強品牌識別度。
‧拋光或噴砂:
表面拋光或噴砂處理,改善手感並提升產品的耐磨性。
‧組裝與包裝:
若製品為多部件組成,進行組裝和包裝,確保交付給客戶的是完整產品。
6. 未來發展趨勢:塑膠射出成型的數位化與自動化
隨著科技進步,塑膠射出成型正朝著數位化和自動化的方向發展。智慧工廠的出現使企業能更高效地管理生產流程,降低成本,提升品質。
‧自動化設備:
透過機械臂及自動檢測系統,可以大幅減少人力需求,提高生產效率和精確性。
‧數據分析:
即時監控生產數據,發現並排除生產過程中的問題,提升生產線的穩定性。
‧綠色製造:
使用環保材料及節能工藝,減少能源消耗及廢料產生,達成企業的可持續發展目標。
塑膠射出成型是複雜且精密的工藝,從射出模具設計、材料選擇、成型工序到後加工,每個環節都影響著最終產品的品質。透過嚴格把控每道工序,企業不僅能夠保證產品的穩定性和耐用性,還能滿足客戶的多樣化需求,提升品牌競爭力。隨著技術的不斷進步,塑膠模具射出成型將繼續成為現代工業製造的中流砥柱。
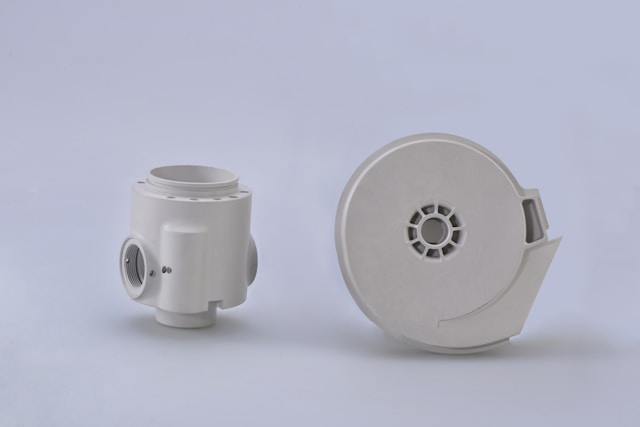
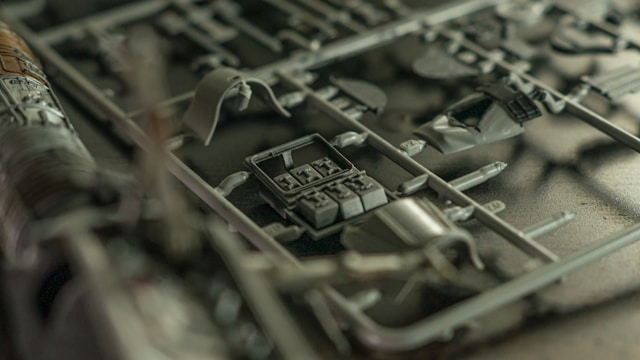